Gas Assisted Injection Molding Solutions
Discover expert gas assisted injection molding for precise, hollow plastic parts with reduced cycle time and improved efficiency.
Why Choose Huazhi for Gas Assisted Injection Molding Solutions?
High-Quality Parts
As an ISO-certified company, Huazhi adheres to ISO 2768 standards to ensure precise tolerances for gas assisted injection molding. Depending on your design requirements, we can achieve tight tolerances up to +/- 0.02mm, delivering high-quality parts with exceptional accuracy.
Fast Lead Time
Huazhi’s advanced gas assisted injection molding process guarantees efficient production and faster lead times. With modern automated facilities, we effectively manage complex custom projects to meet your deadlines.
Engineering Support
With extensive expertise in gas assisted injection molding, Huazhi offers tailored solutions to enhance product durability and reduce manufacturing costs. Our innovative techniques and state-of-the-art machinery ensure each component meets your requirements in quality, functionality, and aesthetics.
Our Awesome Clients
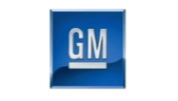
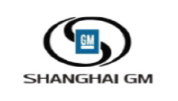
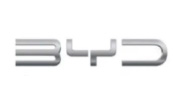
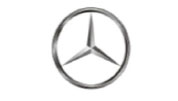
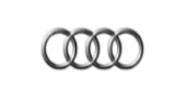
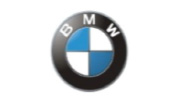
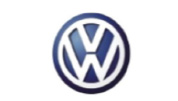
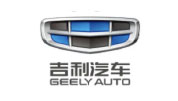
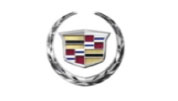
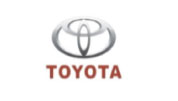
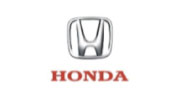
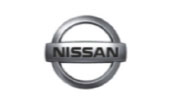
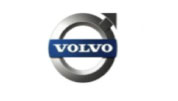
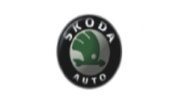
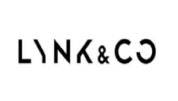
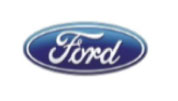
What is Gas Assisted Injection Molding?
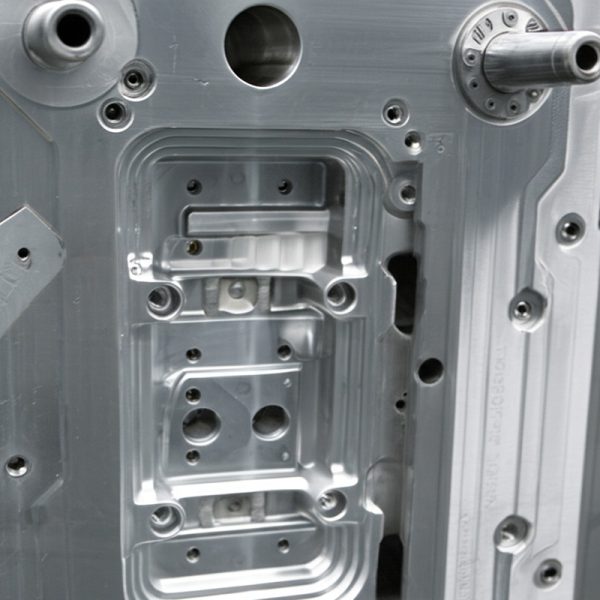
Gas assisted injection molding is an advanced injection molding technique that combines plastic and pressurized gas (typically nitrogen) to fill a mold efficiently. This innovative process offers a significant advantage — the ability to produce hollow parts within the typical cycle time of an injection molding machine.
The gas assisted injection molding process shares similarities with traditional injection molding. First, raw pelletized plastic is melted in the extruder barrel of the injection molding machine. The molten plastic is then injected into the mold, filling it to approximately 70% capacity. At this point, pressurized gas is introduced through a separate entry point. As the plastic cools, the gas pushes the molten material against the mold walls, ensuring uniform thickness and smooth surfaces. Once the part solidifies, the gas pressure is released, and the finished product is ejected just like a standard injection molded part.
This process is ideal for creating hollow plastic components in a single manufacturing step. While alternative methods like blow molding or rotational molding can also produce hollow parts, gas assisted injection molding is often faster and more efficient. Blow molding requires significant capital investment and is primarily suited for high-volume bottle production, while rotational molding typically involves longer cycle times measured in minutes rather than seconds.
Types of Gas Assisted Injection Molding Processes
Internal Gas Assisted Injection Molding
Internal gas assisted injection molding is more widely used than the external method, making it the ideal starting point for discussion.
In this process, molten plastic resin first enters the mold through the sprue channel. Pressurized gas is then injected through a nozzle, forming a bubble within the molten resin. As the gas bubble expands, it pushes the molten resin tightly against the mold walls, allowing the part to take shape.
This method is particularly effective for creating hollow, lightweight geometries. Additionally, the constant pressure exerted by the gas minimizes shrinkage and warping, which are common issues in thin-walled parts. As a result, internal gas assisted injection molding is well-suited for manufacturing thin-walled components requiring precision and structural stability.
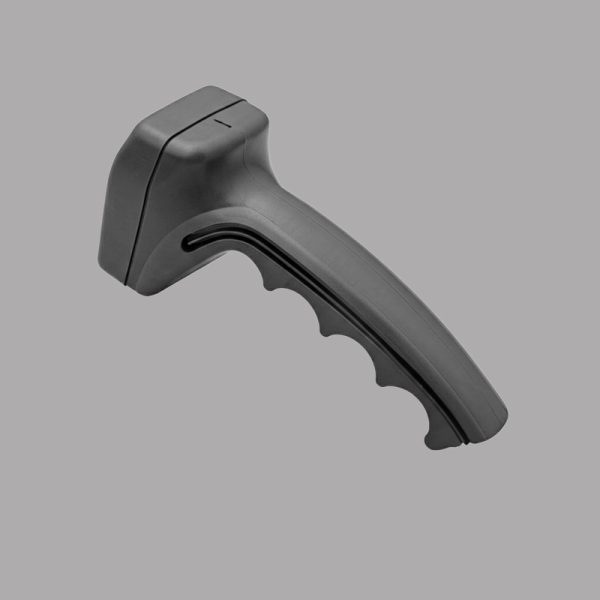
External Gas Assisted Injection Molding
External gas assisted injection molding differs significantly from the internal process. In this method, gas does not penetrate the material to form a hollow section. Instead, the gas is introduced through micro-channels, applying pressure only on one side of the mold.
By exerting pressure from the non-visible or backside of the component, molten resin is firmly pressed against the mold’s detailed surface.
This technique is renowned for producing parts with superior surface finishes. Since the gas applies even pressure to the non-visible side, the visible surface achieves a flawless finish with precise details, including fine mold textures and patterns. For parts requiring intricate designs, imprints, or surface patterns, external gas assisted injection molding is the preferred choice.
What are the advantages of Huazhi

120+
Advanced Equipment
Introduction the world's leading precision machinery, improving manufacturing capabilities, setting standards for precision and excellence, and providing customers with versatile and high-quality production services.
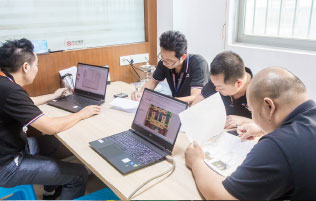
180+
Technical Staff
Our team covers multiple professional fields from engineering to mold design, quality control and project management, creating comprehensive professional technical capabilities to ensure efficient project completion.
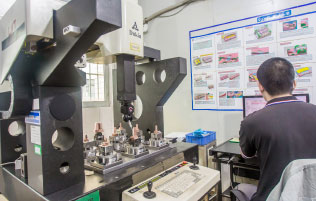
20+
Experience
With more than two decades of accumulated expertise and successful cases, we stay ahead in manufacturing innovation and provide customers with consistently high-quality and reliable products.
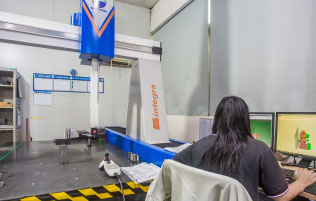
30+
Served Countries
Huazhi Mould has established a solid business in more than 30 countries, including the United States, Germany, Japan, the United Kingdom and India, and strictly abides by international standards.
Find High-Quality Gas Assisted Injection Molding Solutions?
Partner with a trusted expert to reduce lead times and enhance your manufacturing efficiency. Get a free consultation today! Click below to inquire now and let’s create the perfect mold for your needs.
Advantages and Disadvantages of Gas Assisted Injection Molding
Advantages of Gas Assisted Injection Molding
Gas assisted injection molding offers several key benefits compared to traditional injection molding, thanks to its unique process:
Reduced Warpage
By distributing pressure through internal hollow air channels, this method minimizes internal stress, effectively reducing product warpage.
Eliminates Sink Marks
The internal pressure created by gas channels prevents sink marks, which are often caused by uneven shrinkage in thicker parts like ribs and bosses.
Lower Clamping Force
Gas assisted injection molding requires reduced holding pressure, lowering clamping force requirements by 25% to 60%.
Material Savings
This process can reduce material usage by up to 35% compared to conventional methods, thanks to the creation of hollow parts and minimized gate material.
Shorter Cycle Time
By displacing thicker core material, cooling time can be reduced by up to 50%, accelerating production cycles.
Extended Mold Life
Lower injection and holding pressures reduce mold stress, minimizing maintenance needs and extending the mold's lifespan.
Disadvantages of Gas Assisted Injection Molding
Despite its numerous advantages, gas assisted injection molding also presents certain challenges:
Increased Process Complexity
The process involves a complex interaction between polymer melt and high-pressure gas, requiring precise control and expertise.
Complex Mold Design
This method demands intricate mold structures, along with highly skilled operators and experienced process engineers to ensure precision.
Higher Initial Investment
Implementing gas assisted injection molding requires specialized equipment, customized molds, and purified nitrogen, contributing to higher startup costs.
How To Work With Us
The gas assisted injection molding process may seem simple, but there are many parameters that need to be tightly controlled to ensure the quality and consistency of the plastic components produced.
Submit Your Request
To receive a free quote, simply provide a product description along with a technical drawing. If you don’t have a drawing, don’t worry—we offer reverse engineering services to help you get started.
DFM Analysis & Quotation
We typically respond within 24 hours, providing a Design for Manufacturability (DFM) analysis and a detailed quote. Open communication is key, and we offer unlimited discussions at no cost to ensure the best solution for your project.
Precision Mold-Making
Once the design is approved, we begin crafting your custom injection mold tooling using state-of-the-art equipment. Our advanced processes ensure a high-precision mold tailored to your exact specifications.
Injection Molding
After mold completion, we initiate the injection molding process, ensuring each plastic part is consistent, durable, and accurate. Our strict quality control measures guarantee optimal performance for every batch produced.
FAQs About Gas Assisted Injection Molding
Gas assisted injection molding requires precise control throughout the process. Without experienced operators and trained technicians, the risk of errors increases, potentially leading to severe consequences. Achieving high-quality, functional parts demands careful management of multiple variables to ensure successful results.
Gas assisted injection molding accelerates the cooling process since there’s no molten core to solidify. This allows components to be ejected faster. Additionally, this method enhances dimensional accuracy and improves surface quality. It also effectively eliminates sink marks caused by inconsistent wall thickness.
In external gas assisted injection molding, molten resin is first injected into the mold. Gas is then introduced in a micro-thin layer between the back surface of the part and the mold core. This forces the front surface of the part tightly against the opposite side of the mold cavity, ensuring a smooth and precise finish.
During the injection molding process, air escapes through specially designed venting channels and the natural gaps found at mold parting lines. These features help prevent air entrapment and ensure smooth material flow.
ABS Plastic: Known for its durability and impact resistance, ABS plastic molds can last approximately 100,000 to 300,000 cycles.
Polycarbonate: Valued for its strength and clarity, polycarbonate molds typically achieve 100,000 to 200,000 cycles before requiring replacement.
The ten most common defects in injection molding include:
Flow lines
Sink marks
Surface delamination
Weld lines (knit lines)
Short shots
Warping
Jetting
Vacuum voids
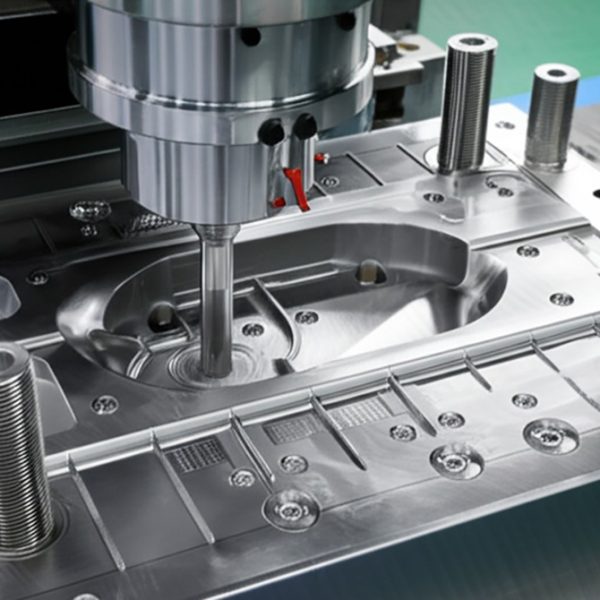
Quality
Certifications
Huazhi has many patent certificates and strictly implements international quality control standards in production to ensure product quality. It has passed IATF16949, lSO 9001, lSO4001, lSO45001 certifications.
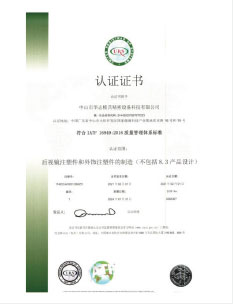
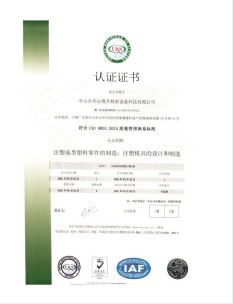
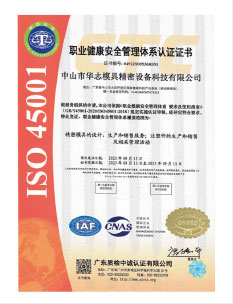
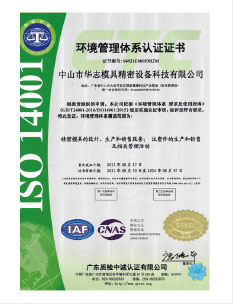
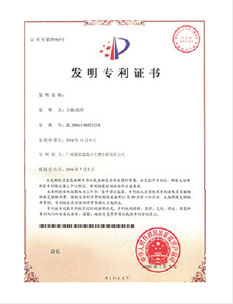
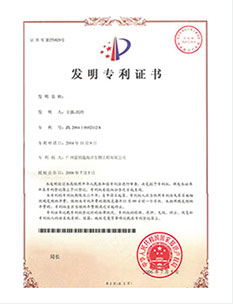
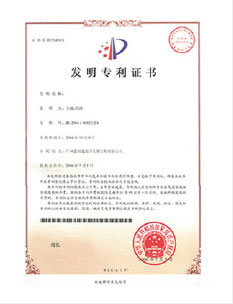
Related Resources
Get a Free Consultation Now
If you have any questions about gas assist injection molding projects, or you are looking for China gas assist injection molding suppliers, welcome to contact Zhongshan Huazhi for more information. Our experienced engineering team will provide professional suggestions and solutions for your gas assist injection molding suppliers project based on your CAD and step diagrams.