Injection Mold Tooling Service
Injection mold tooling for high-quality plastic parts with ±0.02mm precision. Huazhi delivers reliable, custom solutions to optimize your production.
Why Choose Huazhi for Injection Mold Tooling Services?
High-Quality Parts
As an ISO-certified manufacturer, Huazhi ensures exceptional injection mold tooling with precision tolerances tailored to your needs. We achieve tight tolerances of up to ±0.02mm based on your design, guaranteeing high-quality molded parts.
Fast Lead Time
Leveraging certified domestic factories and a robust supply chain, we streamline the injection mold tooling process to accelerate your product development cycle, ensuring rapid production of your injection-molded parts.
Engineering Support
With extensive expertise in diverse molds and applications, our team provides professional guidance and customized injection mold tooling solutions to help you optimize production and achieve your business goals.
Our Awesome Clients
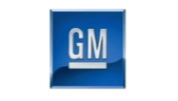
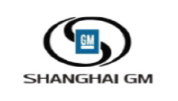
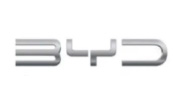
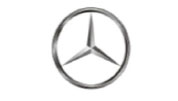
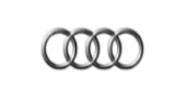
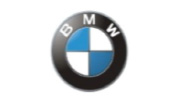
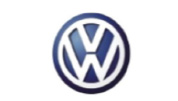
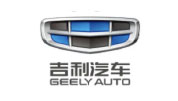
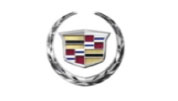
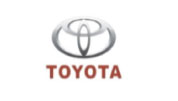
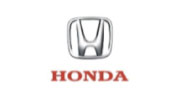
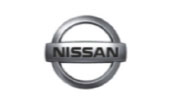
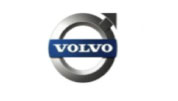
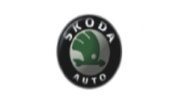
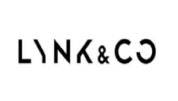
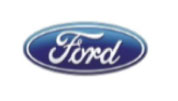
What is Injection Molding Tooling?
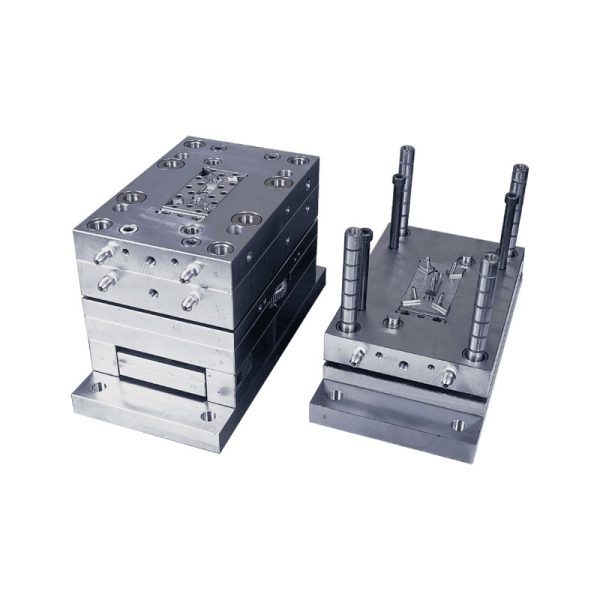
Injection molding tooling refers to the detailed and complex process of designing and manufacturing the tools required for producing plastic or metal parts through injection molding.
This tooling process is multifaceted, involving the creation of durable and highly precise molds that can withstand the rigorous demands of high-volume production. These molds, typically made from robust materials such as steel or aluminum, must endure extreme pressure and temperature during the molding process. Their design and fabrication require advanced expertise, making mold engineering a unique combination of art and science.
At Huazhi, we specialize in injection molding tooling, ensuring that your injection-molded parts are manufactured with the highest precision. We collaborate with you to understand the unique requirements of your project and develop custom mold designs tailored to your specifications. Our skilled technicians handle every aspect of mold production, solving complex challenges to guarantee a seamless manufacturing process.
Our versatility allows us to develop both prototype tools and production molds at competitive prices. With rapid turnaround times, we help optimize your production and accelerate your time-to-market. Ready to take your plastic part manufacturing to the next level? Huazhi is here to support you with expert injection molding tooling solutions.
What are the advantages of Huazhi

120+
Advanced Equipment
Introduction the world's leading precision machinery, improving manufacturing capabilities, setting standards for precision and excellence, and providing customers with versatile and high-quality production services.
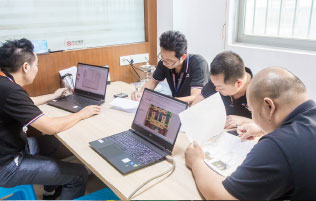
180+
Technical Staff
Our team covers multiple professional fields from engineering to mold design, quality control and project management, creating comprehensive professional technical capabilities to ensure efficient project completion.
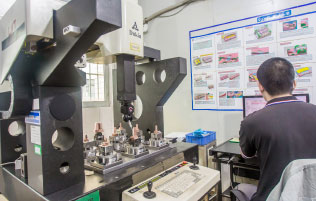
20+
Experience
With more than two decades of accumulated expertise and successful cases, we stay ahead in manufacturing innovation and provide customers with consistently high-quality and reliable products.
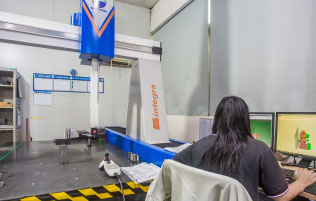
30+
Served Countries
Huazhi Mould has established a solid business in more than 30 countries, including the United States, Germany, Japan, the United Kingdom and India, and strictly abides by international standards.
Find High-Quality Injection Mold Tooling Services?
Partner with a trusted expert to reduce lead times and enhance your manufacturing efficiency. Get a free consultation today! Click below to inquire now and let’s create the perfect mold for your needs.
Quality Control Center – Injection Molding Product Inspection
At Huazhi Mould, we ensure the highest precision and quality in every project. Our advanced inspection equipment guarantees strict adherence to specifications throughout the injection molding tool making process. With high-precision CMMs, optical projectors, hardness testers, and other cutting-edge measuring tools, we verify dimensional accuracy, material properties, and mold performance. This rigorous quality control helps us deliver reliable and high-performance molds, optimizing your production efficiency.
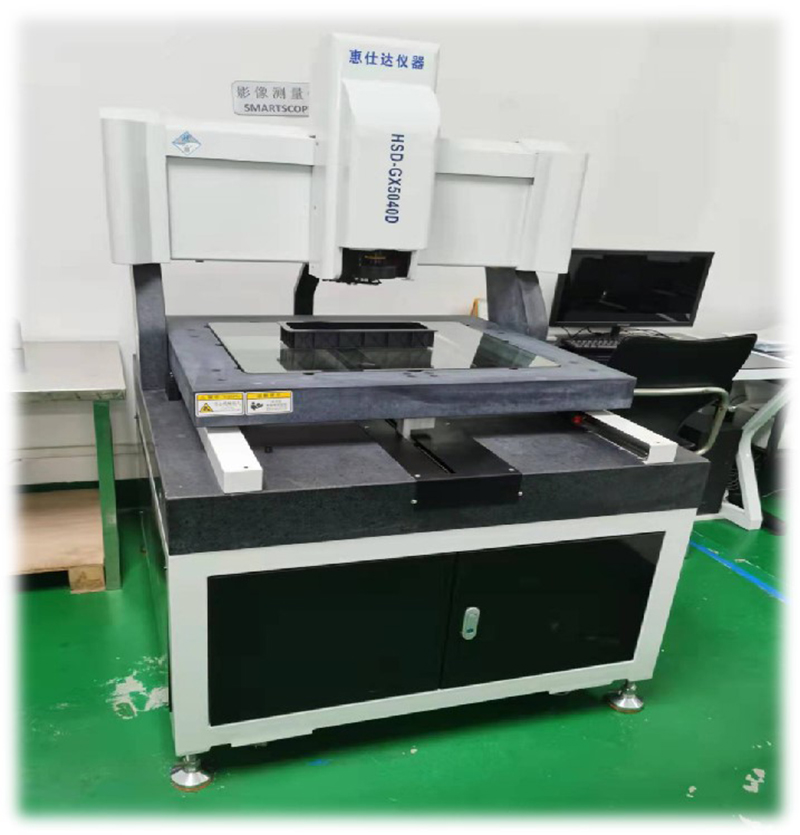
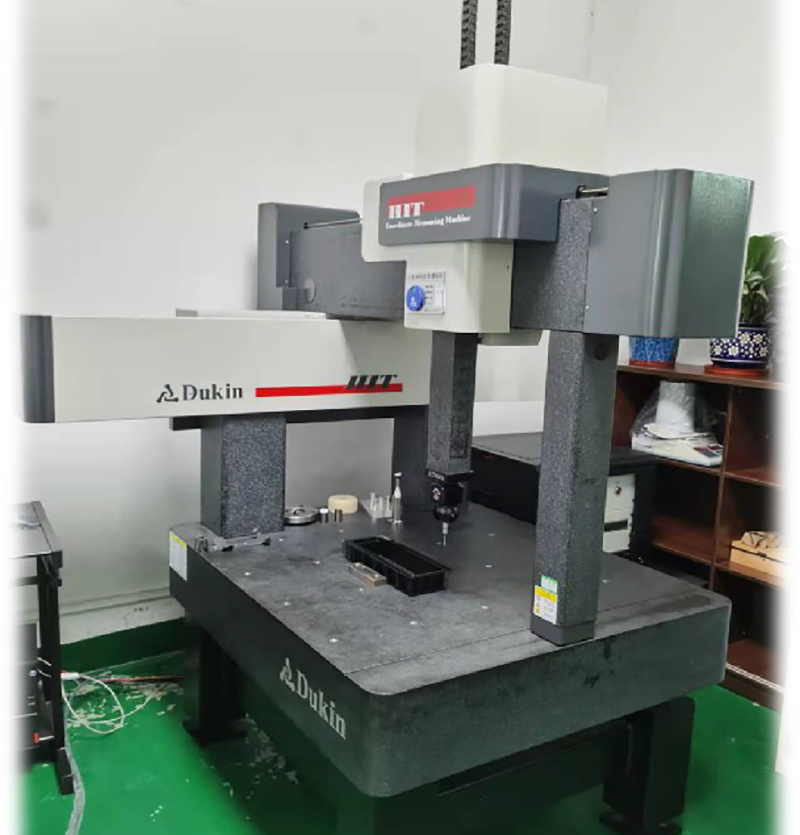
How To Work With Us
The plastic injection molding process may seem simple, but there are many parameters that need to be tightly controlled to ensure the quality and consistency of the plastic components produced.
Submit Your Request
To receive a free quote, simply provide a product description along with a technical drawing. If you don’t have a drawing, don’t worry—we offer reverse engineering services to help you get started.
DFM Analysis & Quotation
We typically respond within 24 hours, providing a Design for Manufacturability (DFM) analysis and a detailed quote. Open communication is key, and we offer unlimited discussions at no cost to ensure the best solution for your project.
Precision Mold-Making
Once the design is approved, we begin crafting your custom injection mold tooling using state-of-the-art equipment. Our advanced processes ensure a high-precision mold tailored to your exact specifications.
Injection Molding
After mold completion, we initiate the injection molding process, ensuring each plastic part is consistent, durable, and accurate. Our strict quality control measures guarantee optimal performance for every batch produced.
FAQs About Custom Injection Mold Tooling
Choosing the right material for custom injection mold tooling affects durability, cost, and performance:
- Steel: Preferred for high-volume production due to wear resistance (e.g., stainless steel, P20, H13).
- Aluminum: Ideal for prototyping and low-volume runs, offering faster heating and cooling cycles.
- Beryllium Copper: Used in areas requiring rapid heat dissipation and intricate details.
- Pre-Hardened Steel: Cost-effective for lower-demand applications, eliminating the need for extra heat treatment.
- Tool Steel: Suitable for high-wear applications, offering toughness and longevity.
- Nickel-Based Alloys: Used in high-temperature molding applications like insert molding.
Several factors impact custom injection mold tooling design:
- Part Geometry & Complexity: The shape, size, and intricate details of a molded part influence mold features, requiring specialized gating, cooling channels, or ejection mechanisms.
- Material Selection: Different plastics affect cooling rates, shrinkage, and flow behavior. For example, polypropylene has higher shrinkage, while polycarbonate requires higher mold temperatures.
- Tolerance & Precision: Tight tolerances increase mold complexity and cost, especially in industries like automotive and medical that demand high precision.
- Ejection System: The method used to remove parts from the mold, such as ejector pins, air blasts, or stripper plates, affects cycle time and part integrity.
- Gating Design: Gate location and type (direct, pin, or edge gate) impact melt flow, surface finish, and cycle time.
- Undercuts & Parting Lines: Features like undercuts may require side actions or lifters, increasing mold complexity and cost.
Several factors contribute to the high cost of custom injection mold tooling:
- Material Costs: High-quality materials like hardened steel or aluminum ensure mold longevity but add to expenses.
- Complex Manufacturing Processes: Precision machining, EDM (electrical discharge machining), and manual polishing require advanced technology and skilled labor.
- High Precision Requirements: Industries such as aerospace and medical demand tight tolerances, increasing mold complexity.
- Customization: Every mold is uniquely designed for a specific part, increasing development time and costs.
- Engineering & Design Time: Mold designs must withstand high pressures and temperatures, requiring expert engineering and extensive planning.
The production timeline for custom injection mold tooling depends on factors like mold complexity, part design, and material selection. A simple prototype mold can take 2-4 weeks, while high-precision production molds may require 6-12 weeks. Additional features such as multi-cavity design, side actions, or intricate cooling systems can extend the manufacturing time.
At Huazhi Mould, we follow a strict quality control process for custom injection mold tooling to guarantee precision and durability. This includes:
- Material Selection: Using high-grade steel or aluminum for longevity and wear resistance.
- Advanced Machining: Utilizing CNC, EDM, and high-precision grinding to meet tight tolerances.
- Comprehensive Testing: Conducting mold flow analysis, dimensional inspections, and trial runs to ensure flawless part production before mass manufacturing.
The cost of custom injection mold tooling is influenced by:
- Mold Material: High-grade steel molds last longer but are more expensive than aluminum.
- Part Complexity: Intricate geometries, tight tolerances, and multi-cavity molds increase production costs.
- Production Volume: High-volume molds require robust designs to withstand extended production cycles.
- Design & Engineering: Custom mold development requires skilled expertise to optimize performance and minimize cycle times.
By carefully planning the mold design and material selection, manufacturers can balance quality and cost efficiency.
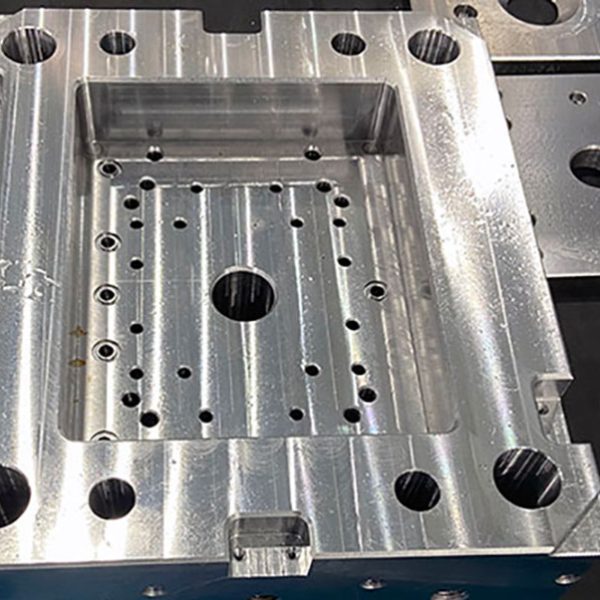
Quality
Certifications
Huazhi has many patent certificates and strictly implements international quality control standards in production to ensure product quality. It has passed IATF16949, lSO 9001, lSO4001, lSO45001 certifications.
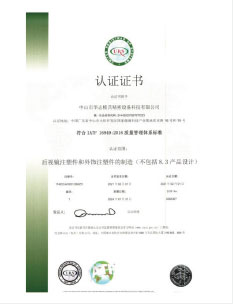
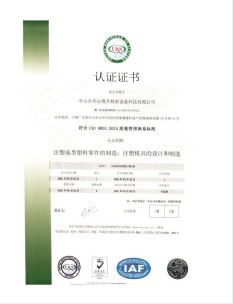
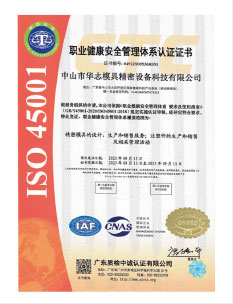
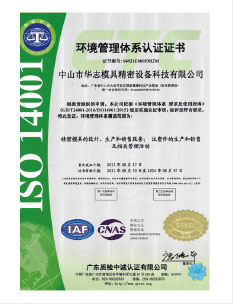
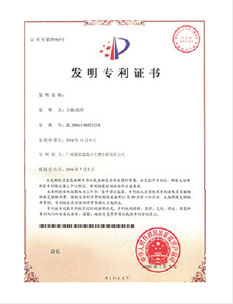
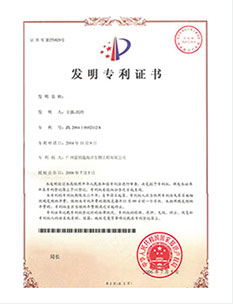
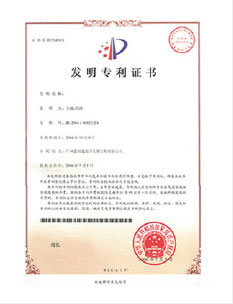
Related Resources
Get a Free Consultation Now
If you have any questions about your injection mold project, or you are looking for a Chinese injection mold manufacturer, welcome to contact Zhongshan Huazhi for more information. Our experienced engineering team will provide professional advice and solutions for your injection mold project based on your CAD and step drawings.